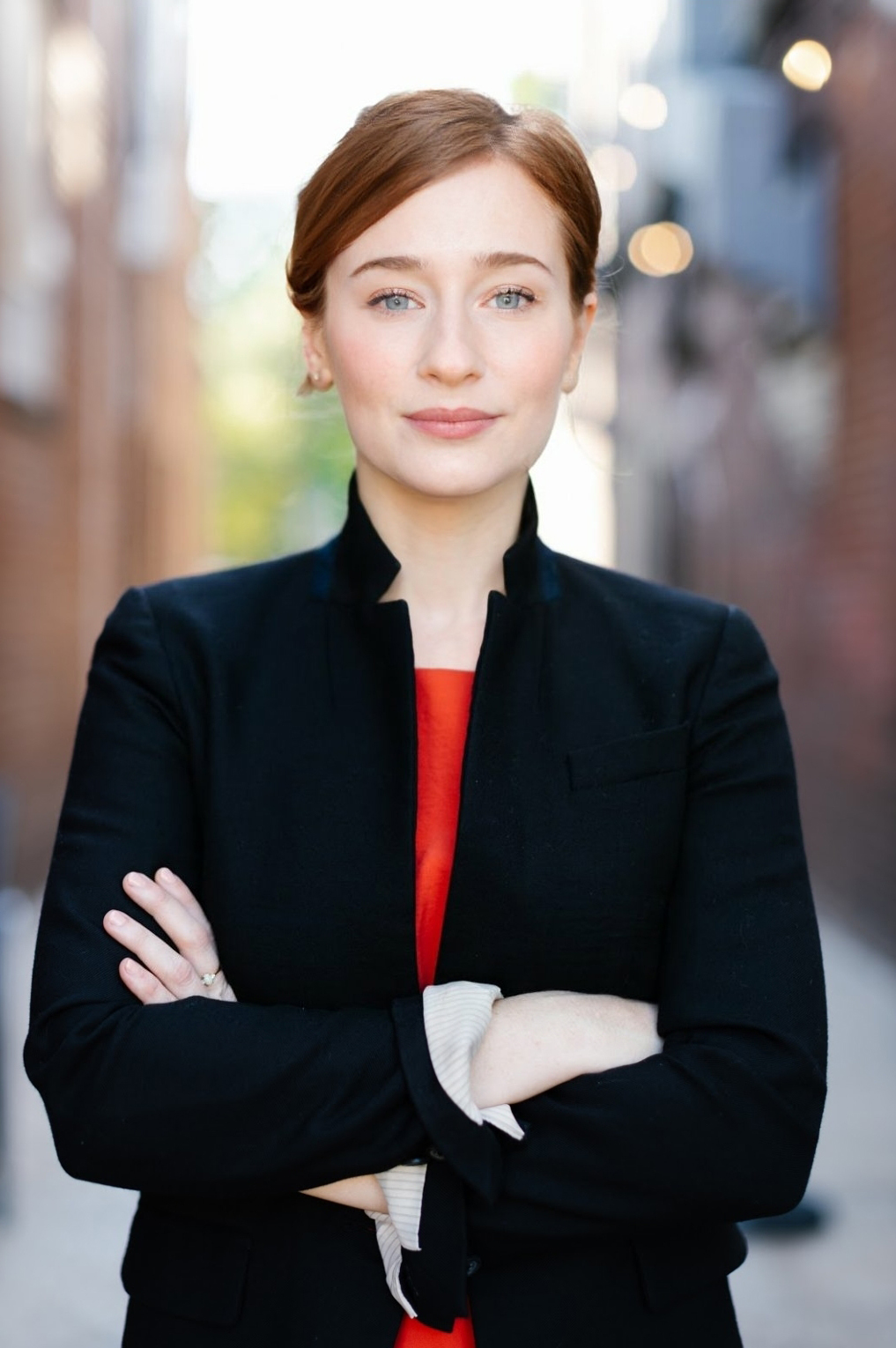
The Top Uses of Digital Technology in the Construction Industry
Construction isn’t a particularly high-tech industry, or at least it hasn’t been until recently. Historically, the sector has been slow to adopt new technologies, either from a lack of demand or prohibitive upfront costs. As digital tech like project management has skyrocketed in the past few years, that’s starting to change.
Digital tools like project management software are both affordable and versatile. They address too many issues too effectively for the industry to ignore them. Throughout every phase of the construction process, these technologies are reshaping the sector.
Here are five of the top uses of digital technology in construction.
Budgeting and Resource Management
The construction industry is notorious for going over budget and over time. According to one report, large projects typically go 80% over budget and fall 20% behind schedule. This is a multifaceted issue, but a lot of it is due to poor planning. Project management software can help.
These software tools streamline the preconstruction phase, saving time, which saves money. More notably, they offer more advanced, in-depth budgeting and resource management solutions. Project management software can analyze historical and current data to predict how much a project may cost and where companies can adjust to make savings.
After producing a more realistic budget, this software can help construction companies stay within it. Automatic reporting, time tracking and invoicing tools keep track of resources, so workers don’t have to. On top of streamlining these processes, these tools improve visibility, helping teams see when and where they may go over budget.
Modeling
Every construction project, no matter the size or significance, needs a thorough design and planning phase. Traditionally, companies have relied on physical models and 2D blueprints to conceptualize and plan buildings. Digital technologies have started to replace these older methods, making this process more in-depth and collaborative.
Building information modeling (BIM) enables architects and other stakeholders to create 3D, interactive digital models of projects. This software allows for faster, easier collaboration in the planning phase and can update in real-time during construction. Project managers can then see and respond to any unforeseen developments without having to be on-site.
Safety
Workplace safety is vital in every industry, but it’s especially crucial in construction. Safety hazards are common in the sector, and with all the heights and heavy machinery involved, accidents can be severe. Digital technologies provide construction teams with the tools they need to stay safe.
The second-most common OSHA violation in construction is hazard communication, with more than 4,000 violations a year. Project management software makes communicating with employees and stakeholders much easier. When someone recognizes a potential hazard, they can use these tools to share it with everyone else, avoiding mistakes from miscommunication.
During the planning phase, digital models can also highlight potential safety issues. Teams can then make adjustments to prevent hazards before they arise. At the worksite, sensors and wearables can help managers keep track of potential dangers and worker health.
Equipment Maintenance
Construction projects rely on heavy equipment, and these machines require a lot of maintenance. If workers don’t take proper care of them, they could malfunction or break, endangering employees, delaying completion times and raising costs. Today, construction teams can use various digital tools to ensure proper maintenance.
Hot weather can lead to overheating and other heat-related problems, but project management software can help teams schedule around the hottest times of the day. Similarly, these digital tools make it easy to establish and keep track of maintenance schedules. They can automatically highlight scheduling conflicts and alert managers when an employee failed to perform a maintenance check.
Other digital technologies, like IoT sensors, can alert workers when a machine may need maintenance soon. They can then address the issue before it leads to a costly breakdown. Since equipment downtime alone can cost $3,120 a year per machine, these digital tools can lead to considerable savings.
Documentation and Reporting
Paperwork might not be what immediately comes to mind with construction, but it’s a factor in any project. Manual documentation and reporting is typically slow and tedious, costing money and taking workers’ focus from more pressing needs. Some project management software solutions can automate this process.
As much as 88% of spreadsheet data contains errors, mostly due to human mistakes. Automating the process removes many of these issues since computers are typically better at data-heavy tasks than people. They’re also faster, so project management software can help companies save time on paperwork.
Digital Tech Is Transforming Construction
As more companies use this technology, others will realize its benefits and do the same. Before long, the entire construction industry will rely on project management software and other digital tools. A sector that was once resistant to change will become as tech-centric as anything else.
Construction has become infamous for problems with efficiency and budgets. Digital technology offers an answer. These resources will transform the industry, making it safer, faster, more collaborative and profitable.
This blog was guest authored by Rose Morrison. Rose Morrison is a construction industry writer and the managing editor of Renovated. Follow her on Twitter to see more of her work